3DプリンターABS樹脂を使いこなそう
3Dプリンター用の樹脂といえば、PLA樹脂と、ABS樹脂ですよね。ちょっと強度の必要なものを作ろうと思うと、ABS樹脂を選びたいのですが、反ってしまったり、割れてしまったり。
この記事では、ABS樹脂の特性を学び、反る原因を潰し、うまく造形できる方法を解説したいと思います。
ABS樹脂の特性を学び失敗しない造形方法を確立しよう
ABS樹脂がうまく造形できないのはABS樹脂の熱収縮が原因
ABS樹脂は、熱収縮率が大きいため反ったり割れてしまったりするようです。
熱収縮が一体どんなものかというと、射出した直後のサイズから冷えると小さくなる現象です。日常的にみるほとんどの物質は温度が高いと大きくなり、冷めると小さくなります。水は例外ですが。
メカニズムが分かったところでABS樹脂で造形すると反ってしまうか考えてみよう
このメカニズムが分かったところで、実際の積層中にはどんなことが起こってるの考えてみますと
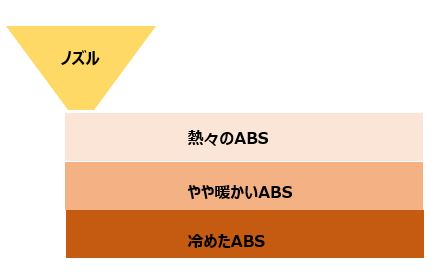
積層していくと、ABS樹脂の温度は最初に積層したものほど冷えていますよね。ノズルに近いところほど温度が高く、熱々です。
ここから少し冷えたのが次の図です
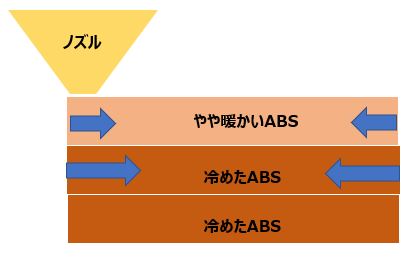
熱かったABS樹脂が冷えると、熱収縮で青矢印で示すように小さくなろうとします。そうすると、一番下のABS樹脂の層は上に積層されたABS樹脂の熱収縮に誘われて、上の段に触れている側が縮んでしまいます。こうなると、一番下の段の積層面は長さがそのままにも関わらす、そのすぐ上の積層面が熱収縮で縮むため次図のように反ってしまうのです。
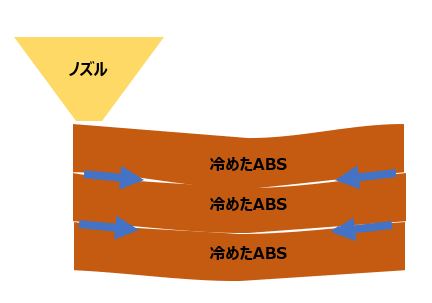
そしてこの現象は、造形が終わるまで繰り返されるので、反ってしまったり、あるいは割れが出てしまうなどの不具合が出てしまうのです。
このメカニズムから考えられる最悪の条件は、先に積層した層が冷たく、そのすぐ上の層が熱々になっている。というのが最も悪い条件になります。
ABS樹脂の上手に造形する5つのポイントを解説
上記のように説明した通り反ったり、割れたりする原因は温度の影響によるものです。ですから温度に対して対策を取ればABS樹脂をきれいに造形できるようになるはずです。
1.造形中は温度を高い状態を保つ
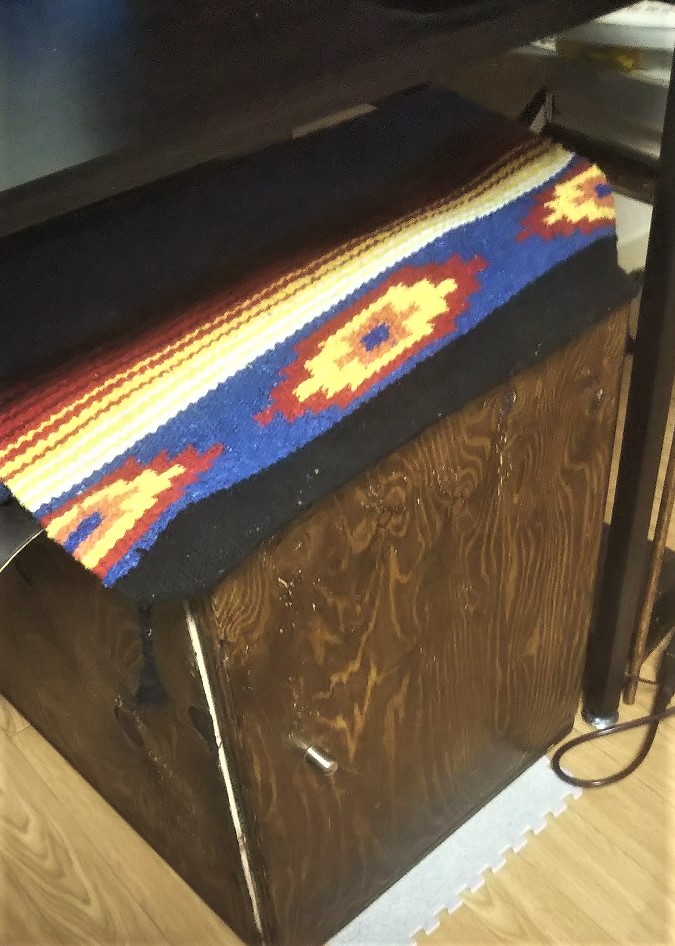
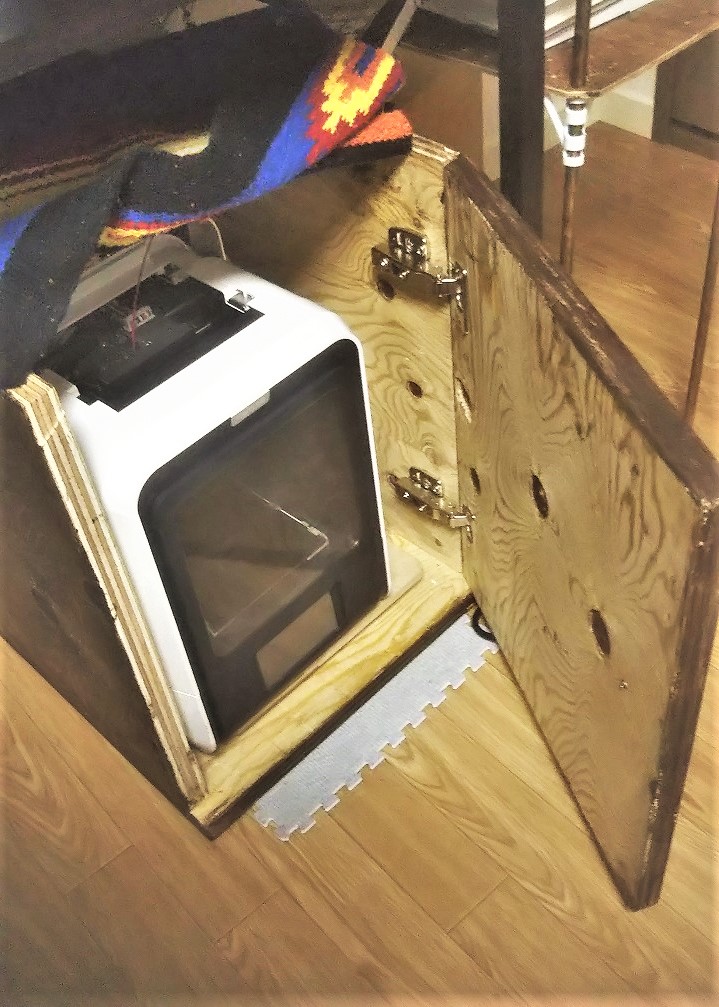
強度の欲しいものを造形したいと考えていて、これから3Dプリンターを購入するのならば、ケースで囲われたモデルを選択肢に入れるべきです。
ケースで囲われたマシンならば、外気温の影響を小さくすることができます。
既に持っている3Dプリンターがケースのないモデルでしたら、これを機にケースを作ってしまうのも選択しの一つかもしれません。合板などで外を囲ってしまうだけでだいぶ温度変化に対して効果が出ます。防音効果も期待できますね。
最近の3Dプリンターは音がすごく小さくなっており、造形サイズも多きなっていて驚きます。
下の写真の一つ前のモデルを使っていますが、サイズも270㎜まで作れるようになり、テクノロジーの進化はすばらしいです。
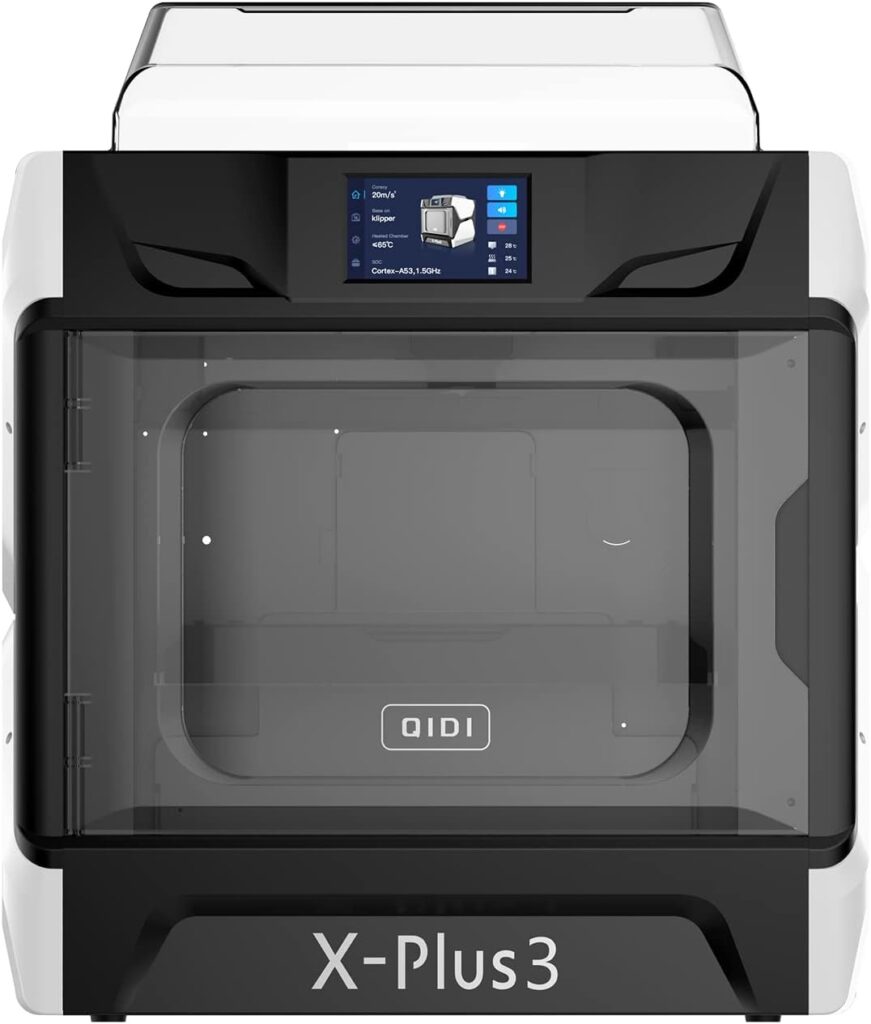
2.ABS樹脂の造形中は冷却ファンを止める
ABS造形時の冷却ファンの使用は極力避けるべきです。もし、プリント後の造形品にヒゲ状のモノがたくさんついているようでしたら、冷却ファンで対策するのではなく、ノズルの温度設定を下げる対策を取りましょう。
3Dプリンターにはノズルに風を吹き付ける機構がついています。機種によっては風を調節できるようになってます。私が使っているUPminiはシャッターがついており、ABSを使用する場合は微風になるように調節しています。PC上だったり、3Dプリンター側の設定でファンの動作を止めるなど機種によってまちまちなので、ご自身のマシンも確認してみましょう。
3.プリントボード(造形面)のプレートは50度以上を目指そう
造形前に加熱できる機能がついている場合、積極的に使いましょう!
私は50度以上を目安にしています。
何が何でも早く造形開始したい!という方はドライヤーで強制的に温めてしまいましょう。ファンヒーターで熱々にしてから造形したこともあります。もちろん3Dプリンターからプリントボードだけを取り出してです。
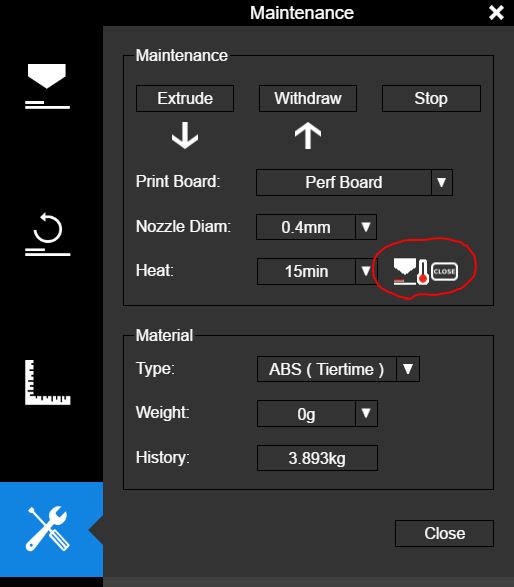
UPminiのソフトでは、予熱ボタンがあります。
4.反りの影響を最小限に抑える造形レイアウト
3.までは、反ることを防ぐ方法を説明しましたが、4では反ってしまっても失敗しないレイアウトについて説明します。
私の経験上、曲面をプリントボード側に向けるのが正解です。
これにはちゃんと理由もあり、冒頭で説明しましたが、ABS樹脂は熱収縮で反ります。では、反ることが しかたないとすれば、プリントボード上に設置したモデルの中で最も反らない場所は造形の中心部になります。
つまり、造形レイアウトで注意するべきポイントは、
- 中心部のみがプリントボードに接地するようにレイアウト
- フラットな面をプリントボードに向けてはいけない
- フラットな面が欲しいときは、側面や上面に向ける
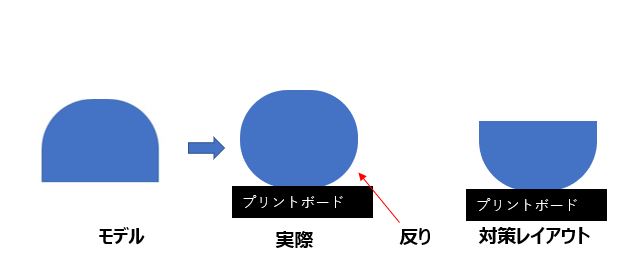
上の図:失敗しにくいレイアウトは右端の曲面をプリントボードに向けたレイアウト
下の図は、ルアーを作った際の画像です。きれいにできるのは、左のレイアウトで、失敗するのは、右の図です。
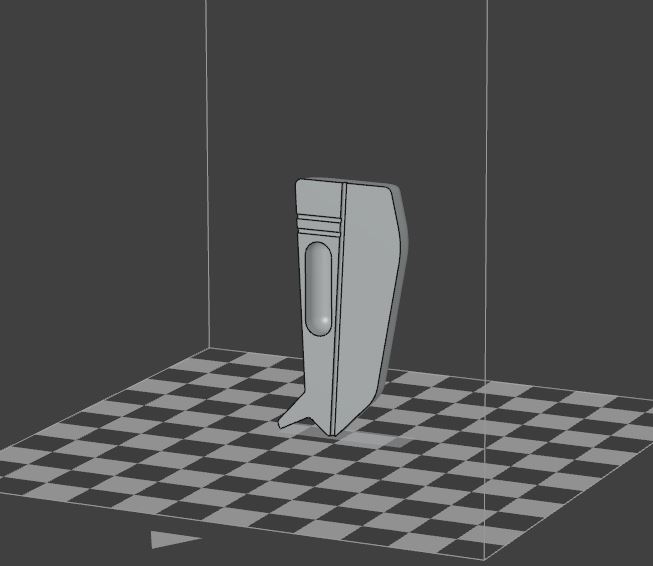
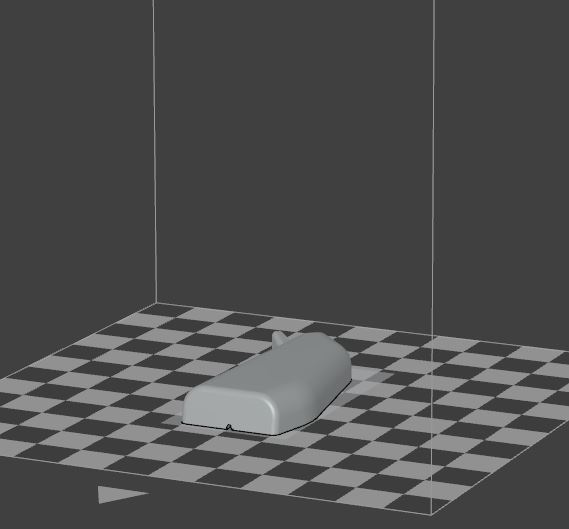
このルアーは、半分ずつ造形して張り合わせるます。この時、張り合わせ面が反っていてはうまくルアーは作れません。
張り合わせ面を平らに造形したいときは、左のように平らの面が側面になるようにレイアウトするときれいに造形できます。
また、ベースの板にも設置する面が少ないほうがきれいに造形できます。
平らな面をプリントボード側にしてレイアウトしたくなりますよね。PLA樹脂ならば、その方法で問題ありませんが、ABS樹脂ではほぼ失敗してしまいます。
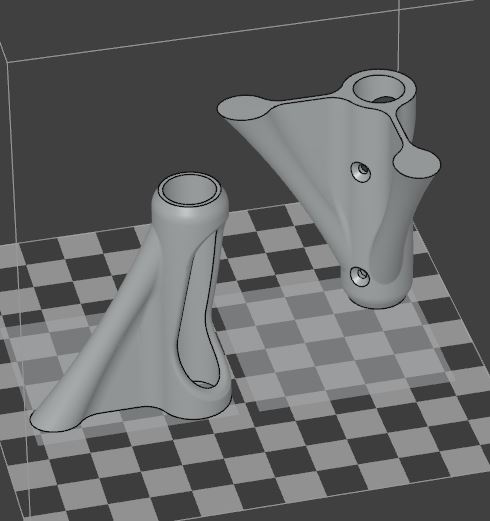
上の図 そりが出やすいレイアウトは左。一見バランスの悪く見える右側のレイアウトの方が、造形での失敗は少ない
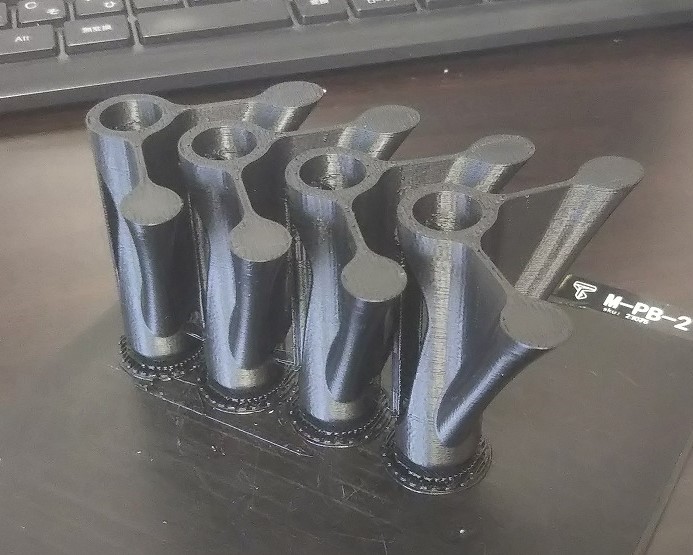
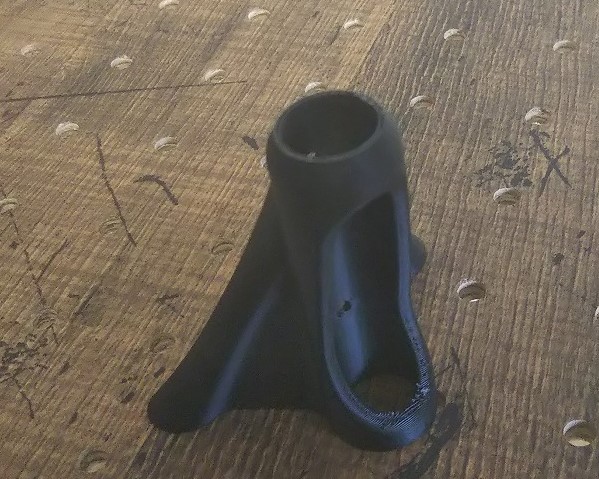
実際に3Dプリンターで造形したもの。プリントボードに接地している部分は、右の写真の上端部、厚みが1㎜程度のリング形状のみ。
5.反りにくいABS系樹脂 ABS+を使う
最も反り対策を樹脂で行うのも一つの手法でしょう
ABS樹脂は反りやすいですが、造形性を改善したABS+という種類もありますのでこちらを選択するほうが無難かもしれません。
最近Amazonでのラインナップが減ってしまい残念です。
失敗しにくいABS樹脂造形のまとめ
- 温度変化しにくい環境を整える
- ファンを止めるめて造形品を冷やさない
- プリントボードを高温にする
- 反りやすいプリントボード面には曲面を向ける
- 材質を見直す
いかがだったでしょうか?もしあなたがまだトライしたことのない方法がありましたら是非トライしてみてください。
条件出しは地味でめんどくさいですが、うまく造形できるとほんとにうれしいです。